Vår värld befinner sig mitt i en betydande utveckling av det sätt på vilket vi tillverkar och producerar varor. Denna omvälvande period kallas den fjärde industriella revolutionen eller Industry 4.0. Industry 4.0 är en trend mot automatisering och datautbyte inom tillverkningsteknik och arbetssätt som omfattar artificiell intelligens (AI), databehandling i molnkanten och anslutningsmöjligheter.
Även om de trender som vi kommer att diskutera här är mycket framåtblickande och futuristiska är många företag helt enkelt inte där ännu. Vi är medvetna om att organisationer befinner sig i olika stadier på denna omvälvande resa, men på samma sätt som alla följde med i den ursprungliga industriella revolutionen (ångdrivna maskiner), den andra ”tekniska” revolutionen (järnvägen och telegrafen) och den tredje (digitala) revolutionen, förväntar vi oss att många av de trender som växer fram under den industriella revolutionen med tiden kommer att bli vardagsmat.
Att se dubbelt
För att möta en ökande global efterfrågan och hantera utmaningar inom försörjningskedjan måste tillverkare tänka framåt. Ett nytt, kostnadseffektivt sätt att göra detta är att skapa en digital tvilling, vilket är en virtuell representation i realtid av ett fysiskt system eller en process som kan agera som en digital motsvarighet för simulering, integration, testning och underhåll. Digitala tvillingar möjliggör detaljerade simuleringar av hårdvara som påverkar allt från tillverkningsprocesser till utformningen av hela fabriksgolvet.
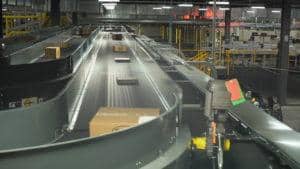
Genom att bygga en maskin, en produktionslinje eller ett lager virtuellt spenderar företaget inga pengar på delar eller utrustning, och den digitala tvillingen kan bekräfta att det kommer att fungera innan investeringar sker. Den digitala tvillingen kan bekräfta hur konstruktionen ska se ut, och när fabriken väl är byggd fysiskt, kan den digitala tvillingen användas för att arbeta vidare med effektivitet och förebyggande underhåll.
På Digi-Keys lager kan vi exempelvis använda vår digitala tvilling för att se hur många packningsstationer som bör vara igång när plockningsstationerna är igång, och beroende på ordervolymen kan vi avgöra om dessa stationer behöver bemannas mer eller mindre. Den digitala tvillingen kan även hjälpa oss att identifiera hur många beställningar som kan hanteras baserat på olika personalnivåer för att konstatera vad som är optimalt.
En annan fördel är förebyggande underhåll och processförbättring. Med en virtuell simulering av den exakta tillverkningsanläggningen kan företag justera saker digitalt och se hur de kan åtgärda eller identifiera problem och problemområden. Varje komponent i en fabrik har en livslängd, och efter en viss tid börjar motorer och delar oundvikligen att krångla och bli elektriskt otillförlitliga. Med en digital tvilling som kör plattformar för förebyggande underhåll kan systemet ge varningar och säga: ”Den här motorn har varit igång i X antal timmar. Vi har börjat se att den vibrerar så här mycket. Och vi vet att när den vibrerar så mycket kommer motorn att gå sönder, om tre veckor, en dag eller om två timmar. Då kan stilleståndstid för byte av motor planeras proaktivt istället för att man drabbas av ett oväntat fel som kraschar hela systemet.
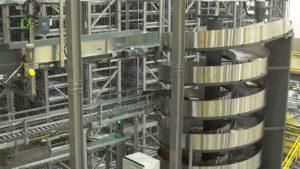
Genom att köra en digital tvilling kan organisationer se framtiden i den virtuella världen innan de tar den i bruk i den verkliga världen. Den digitala tvillingen kan även öka hastigheten och köra t.ex. en veckas tester på en timme, så den har en enorm potential.
Den största tekniska utvecklingen som har gjort digitala tvillingar till en realitet är databehandling i molnkanten, som gör det möjligt att beräkna allting i snabb takt. I takt med att datorkraften ökar över hela linjen kommer dessa metoder att bli allt vanligare. Just nu är kostnaderna för system för att driva databehandling i molnkanten ganska dyra och därför oåtkomliga för många organisationer. Men kompromissen att kunna förutse personalbehovet och veta när systemen behöver bytas ut är oerhört värdefull för fabriksoperatörer. Det sparar tid, och istället för att behöva schemalägga underhåll, vet de faktiskt när systemet kommer att gå sönder och kan förhindra det, vilket förkortar stilleståndstiderna i produktionslinjen.
Användningen av databehandling i molnkanten och digitala tvillingar skapar även fler högavlönade och teknikfokuserade jobb, t.ex. för roller inom informationsteknik (IT), jobb för dataanalytiker med flera. Genom införande av samarbetande robotar på fabriksgolvet, kan dessa ta på sig fler av de tråkiga och monotona rollerna, för att frigöra personal som tidigare utförde dessa jobb för mer värdefulla positioner inom organisationen.
Arbetet måste gå vidare
Oavsett om det handlar om problem med maskiner, komponentbrist eller andra potentiella utmaningar är stopp av tillverkningen helt enkelt inte längre ett alternativ. Dagens fabriker måste uppnå systemövergripande synlighet med hjälp av komplicerade givare och hårdvara som är utformad för att registrera, övervaka och ge viktiga insikter innan problem uppstår.
Det största problemet som anläggningar står inför idag, är bristen på en miljon människor med kvalificerad utbildning som behövs inom automationsområdet, och det kommer bara att bli värre. Så, utmaningen är att hitta de processer som bör automatiseras för att kunna fortsätta arbeta med samma antal personer, men samtidigt växa. Automatisering är skalbar – när du automatiserar något kan du vanligtvis göra det med färre personer eller slippa lägga till fler personer när du växer.
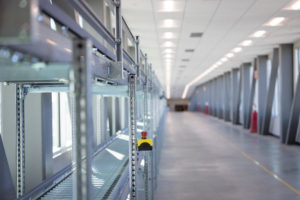
Pandemin tydliggjorde den här trenden eftersom företagen ganska snabbt insåg att de troligen aldrig kommer att kunna rekrytera tillräckligt med arbetskraft för att möta efterfrågan, så utmaningen har blivit att ta reda på vad av det som kan automatiseras som faktiskt sparar pengar. För att bara slänga in en robot för att ersätta en person behöver inte nödvändigtvis åtgärda något eller ersätta behovet av personen.
Det finns även ett stort behov av systemintegratörer som hjälper tillverkare att avgöra vad som kan automatiseras och hur alltihop kan fungera smidigt tillsammans. Studenter bör absolut utbilda sig inom automation och ta reda på hur de kan få jobb som integratörer, eftersom de då är förberedda för framtida arbete.
Tänka utanför boxen
Pionjärer inom tillverkningsindustrin tänker alltid framåt och utvecklar prototyper för framtida tekniker i fabriken. Om vi ser framåt kommer det att finnas många kortsiktiga trender som kommer att föra Industry 4.0 från idé till verklighet. Från samarbetande robotar som kan utföra flera uppgifter till det ögonblick då artificiell intelligens och robotteknik smälter samman, tror jag verkligen att detta kommer att bli större än uppfinningen av hjulet.
Efterfrågan på systemintegratörer kommer inte att upphöra, och det kommer att fortsätta att finnas en större drivkraft för lokal tillverkning. Detta är inte bara en amerikansk, utan även en global trend – alla vill att tillverkningen ska ske närmare den plats där produkten ska användas. Och med mer lokal tillverkning kan företag lättare tillhandahålla specialanpassade produkter, engångskonstruktioner och mindre partier.
När vi rör oss mot en mer automatiserad framtid är Digi-Key fast beslutna att ha det du behöver för nästa revolution i din verksamhet. Med mer än 70 000 automationsspecifika delar i lager och 150 000 automations- och styrprodukter har Digi-Key nästan allt du kan tänkas behöva för automatisering, eftersom vi är dina automatiseringsexperter.
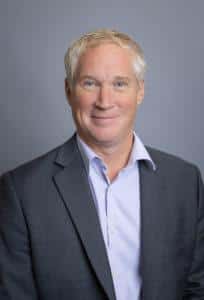
Eric Wendt är chef för automatisering hos Digi-Key Electronics. Digi-Key är både ledande och ständigt innovativa inom distribution av elektroniska komponenter och automatiseringsprodukter med hög service över hela världen, och tillhandahåller mer än 13,4 miljoner komponenter från över 2 300 välkända kvalitetstillverkare.